Mashfrog MES Business Unit launches the RMP Platform
Improving the production performances through a Real-Time control of processes and management parameters is on the agenda with the Real Time Manufacturing Platform of Mashfrog Group.
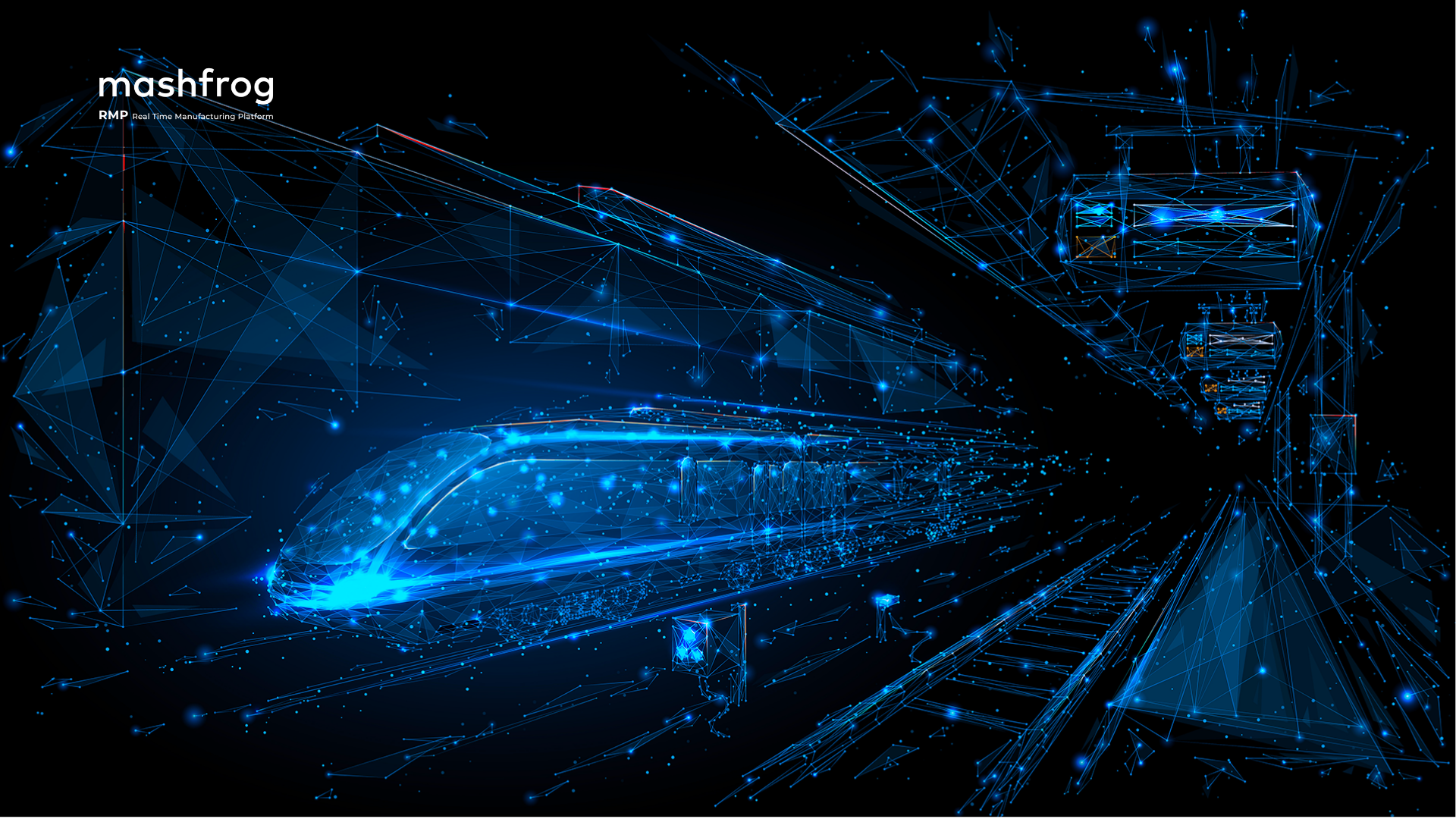
Combining the experience gained by working for companies in the manufacturing sector - in particular in the industry of cables and electrical conductors through the reference in Prysmian Group - to that on development projects and communication with SCADA, HMI, PLC technologies, the MES Business Unit of Mashfrog Group has developed the Real Time Manufacturing Platform (Mashfrog RMP): an interactive dashboard that can be consulted both in the workshop and remotely, which provides a Real-Time representation of the parameters that most affect the production, the so-called Key Performance Indicators (KPIs).
Thanks to its features, the RMP interface fits perfectly into the current context of Industry 4.0, in which a process of digitalization and innovation is underway with a constant search for an end-to-end process improvement, providing support to figures involved in the production, management, and supervision.
The main activities of BU MES
The BU MES (acronym for Manufacturing Execution System) of Mashfrog Group deals with the development of solutions for Industry 4.0 able to support, monitor, manage and optimize the production process, guaranteeing a perfect integration with other tools and actors of the information systems adopted by the company.
Referring to the ISA-95 model, a MES software is located at an intermediate level between sensors and management software (ERP), which plan the resources of the enterprise, being therefore identified as "field agent". This definition arises because MES systems, often being declarative systems, are used directly by the figures present in Shopfloor but at the same time provide the information needed at the management level.
More in detail, a MES software provides visibility, control, and optimization of all business processes related to the production cycle, from the order processing to the finished product. It allows the monitoring of technical data measured by sensors, the flow time, and quality parameters while ensuring the traceability of production lots and raw materials during the process. This information, integrated with the ERP, allows the monitoring of production costs and other parameters necessary for the management of a production system.
The MES can therefore be interpreted as a data bridge between ERP systems and sensors, which nowadays has become indispensable considering the level of innovation, in terms of automation, achieved by companies.
Mashfrog RMP: an interactive and flexible dashboard for controlling the entire production cycle
Specifically, the RMP solution focuses on the control of the production environment and can be adapted both for discrete and process production, in systems with different characteristics and verticality depending on the industry’s type (Automotive, Oil & Gas, Chemical, MILL, etc.). It consists of an interactive dashboard that can be used both via mobile and desktop. The information provided by the RMP ranges from purely technical data (deriving from the PLCs), such as mechanical or thermal efficiency, process speed, temperature, material flow, to management-related parameters, such as the number of working centers, the details of the workers engaged on them, quality performance, and OEE. The tool also allows the consultation of the historical data trend by selecting a reference period, allowing the comparison between different production periods, and then an in-depth analysis of performance. This favors the identification of any aspect of the system on which to make a continuous improvement (a key concept in the model of Lean Manufacturing).
This allows a holistic view of the process: through the increase of control, an immediate identification of possible critical situations is guaranteed. They can emerge both from the monitoring of the technical parameters related to the work centers and therefore a possible anomaly in the machine can be recognized, and from the management parameters which quantify the losses. This facilitates the tasks of all the figures operating in the factory, whether they are engaged in control or working directly in the production chain, having a positive impact also on the maintenance operations management.
Entering the technical details of the solution, our team has pursued the primary objective of developing a flexible solution adaptable to different business contexts and different end-users. To do this, a Python back-end structure has been used for the data processing in terms of sampling, historicization, and format. The front-end is instead developed in C# and JavaScript and provides the KPIs values using appropriate mathematical formulations, through a user-friendly interface. Technically, the solution lends itself to be customized and therefore adapted to different needs and contexts.
Simone Mossa, BU Manager MES, enthusiastically welcomes the development of the new solution: "Mashfrog RMP is just the tip of the iceberg of a more and more complete and integrated business-suite of technologies and services that Mashfrog is able to deliver in Manufacturing. The company is investing heavily in R&D and the development of in-house platforms aiming to manage, in an integrated way, all the core processes of automation and information systems for our customers and prospects”.